Manchester, VT, is something of a time capsule. It’s a two-stoplight town lined with marble sidewalks, manicured lawns, and immaculately restored colonial homes, many of which date back as far as the late 1800s. Driving down the main drag feels like watching a black-and-white movie bloom into technicolor outside your window, and if it weren’t for the occasional Tesla or e-bike sighting, you might actually believe you’d traveled back in time crossing over the New York state line. It’s a stark juxtaposition of old world meets new, which also happens to be the perfect analogy for the township’s most well-known resident, the Orvis fly-fishing shop.
Most anglers, hunters, and wingshooters know Manchester as home to Orvis’ flagship store, a two-story pipedream packed to the gills with premium hunting and fishing gear, but it’s the nondescript wooden building hidden in the back parking lot that’s brought me here today.
I’m speaking about the Orvis Rod Factory, which is the brand’s epicenter for all things fly rod. Every step of the rod creation process from conception to prototyping to production happens right here in the Manchester facility, and it’s something you have to see to believe.
Shall we take a tour?
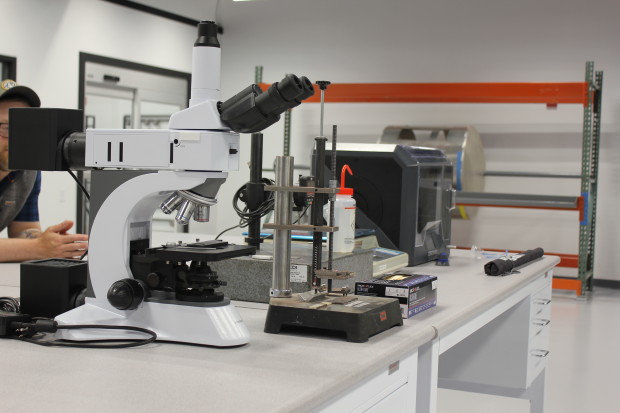
Courtesy Image
Enter Through the Brain Center
“We need to make the world’s lightest fly rod.”
That’s how the modern Orvis fly-fishing rod started some 15 years ago, or at least that’s how Orvis’ director of design and development, Shawn Combs, tells the story. Combs is standing in the middle of Orvis’ newly minted R&D lab, a stark white room loaded down with all manner of laboratory equipment from microscopes and precision scales to electronic ovens and diagnostic computers.
Combs is responsible for the lion’s share of innovation that’s taken place at Orvis over the last decade or so (you can thank him for their current Helios series, for example), which makes sense once you understand his background. See, Shawn has always been a consummate angler, but before fly-fishing paid the bills, he was working at the Knolls Atomic Power laboratory where he designed propulsion systems for nuclear submarines.
Keeping this in mind, I can’t say I’m surprised when Combs takes us for a tour of his pride and joy, the rod testing lab. This portion of the facility comprises Shawn’s custom-built testing equipment, none of which would look out of place in his old nuclear lab.
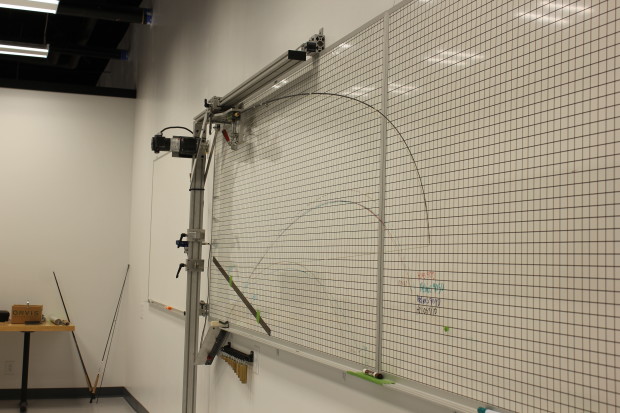
Courtesy Image
It’s here that prototype rods are tested for strength, accuracy, and precision, and hundreds of them are destroyed every year in the name of science. Combs says every time he sets out to design a new rod, he expects to destroy somewhere in the neighborhood of half a million dollars worth of prototypes before he’s satisfied and ready to send a finished product up for production.
I can only watch in horror as he loads a $1,000 fly rod into one of these torture devices, slowly turning the screws to bend the rod past its breaking point. Eventually the rod explodes and swings limply from its station, and I’m left not quite knowing how to feel.
Related: How to Master the Art of Tenkara Fly-fishing
On the one hand, I’m appalled: That rod could have lived a full life pulling trophy fish out of rivers and streams the world over. On another, I’m relieved to know there are guys like Combs out here destroying rods in a lab so we don’t have to break them in the field.
It’s this science-based approach that gave us the Helios 3D Fly Rod, 3F Fly Rod, and 3 Blackout Fly Rod.
Orvis proudly describes these as the most accurate fly fishing tools ever created. There’s no denying the Helios series is positively dripping with innovation, but to understand what truly makes Orvis’ American-made rods unique, we’ll have to head over to the room where they’re produced by the thousands.
Men’s Journal aims to feature only the best products and services. We update when possible, but deals expire and prices can change. If you buy something via one of our links, we may earn a commission.
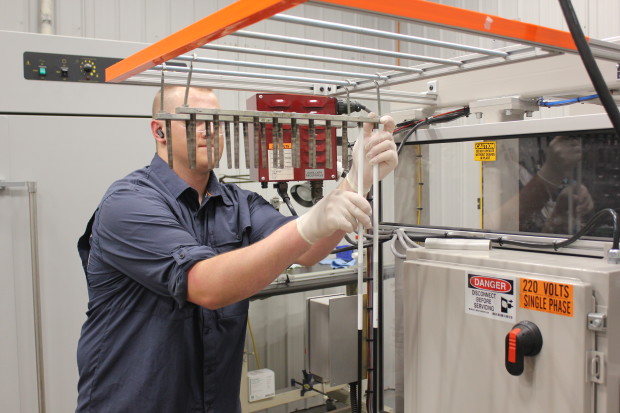
Courtesy Image
Onto the Cutting Floor
Mass production, efficiency, and economy are rarely words we associate with quality or craftsmanship. A walk through Orvis’ fine-tuned production line, however, may change your tune on that subject.
We’re led around the various sections of the factory floor by Don Swanson, Orvis’ Rod Shop manufacturing director, who came to the company from a background in the aerospace industry. Swanson makes no effort to mask his enthusiasm for the production line as he walks us through the manufacturing process one room at a time.
Each step along the way, Swanson highlights the role precision plays in the production of each rod. In one room, sections of carbon are cut with computer-guided razors to ensure complete uniformity. In another, those sections are meticulously inspected before being rolled onto precision-machined mandrels.
Related: The Best Side-by-Side UTVs of 2023
Resin is added and securely wrapped into place by yet another precision machine. Sections are then baked and cooled at precise temperatures in massive ovens to ensure uniform hardness and flexibility.
In the not-so-distant past, each one of these processes was performed by hand with a keen eye for quality. Back then, the performance of a rod depended heavily on the person who put it together, which unfortunately meant that not all rods were created equal.
“It used to be the case that ‘no two rods are exactly the same’ was a good thing,” Swanson says. “Unfortunately that meant if you broke a rod, you were looking at 4-6 weeks of shipping it back and forth to get it repaired, and that’s 4-6 weeks you’re not fishing.”
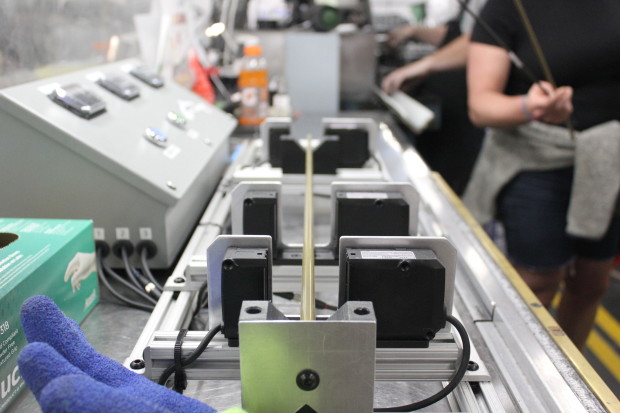
Courtesy Image
Swanson tells us that Orvis’ refined manufacturing processes have improved the tolerances of individual sections of a rod down to 1/1000th of an inch, or roughly one-third the thickness of a sheet of paper. This newly found uniformity means that the individual sections of any two rods are now completely interchangeable, which cuts repair times down to under a week.
Orvis has been quietly utilizing this technology on its American-made rods since 2017 to great effect. Rods made prior to this period, however, do still break and need to be repaired from time to time, which is why you’ll still find an entire wing of the factory floor dedicated to legacy rod repairs as well.
It’s here that highly skilled workers build and repair rods using traditional methods, which is how Orvis remains faithful to its “25-year warranty” while also embracing these new manufacturing processes. Seeing a technician restore a 20-year-old rod to like-new condition is an incredibly satisfying thing to watch, but when it comes to old-world craftsmanship, nothing compares to our final stop on the tour.
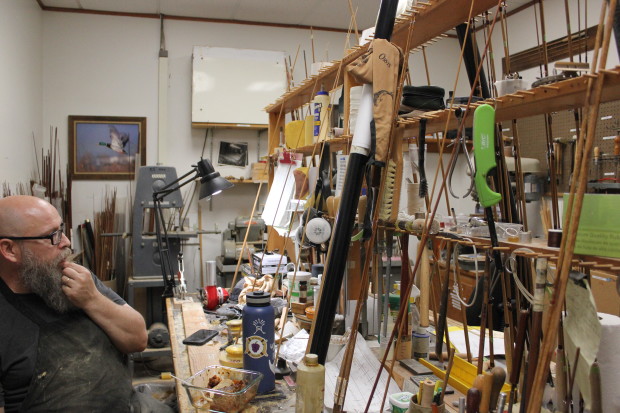
Courtesy Image
Welcome Back to 1946
In an age where robots perform open heart surgery, cars drive themselves, and AI fakes its way through deep discussions, there’s something strangely therapeutic about seeing human skills that can’t be replicated. Here at Orvis, you’ll get that therapy in the bamboo room, a 200-square-foot workshop where rods are still made entirely by hand using centuries-old techniques.
Interestingly enough, this entire operation revolves around the skills of a single man. His name is Shawn Brillon, and he’s the only person in the Rod Shop who knows how to build Orvis’ bespoke line of bamboo rods from scratch.
To hear Brillon describe his process is truly awe-inspiring. He starts with raw bamboo strips, splitting and selecting specific pieces for their strength, color, and appearance. He then cuts, mills, and shapes each piece himself using a combination of hand tools, milling machines, and lathes, all of which have been around the Orvis facility since the 1940s.
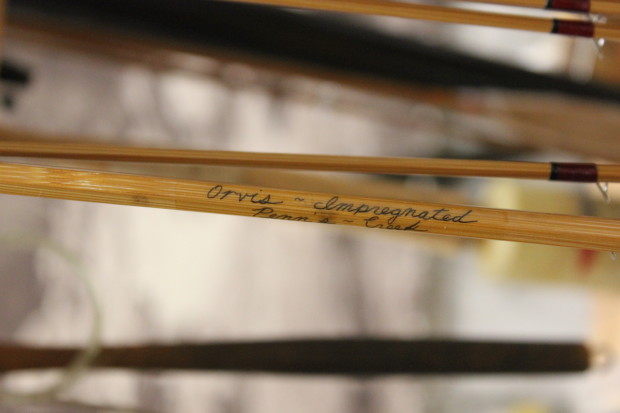
Courtesy Image
From here, Brillon glues, binds, bakes, and tests every single section of rod himself. From start to finish, Brillon is the only person to touch an Orvis bamboo rod right up until it’s deemed ready for its final winding and six coats of high-gloss varnish.
He estimates that crafting a single 1856 model rod involves anywhere from 30 to 40 hours of work on his part, and because he’s the only person in the facility with the skills to do the job, the total production of bamboo rods is limited to roughly five finished rods every month.
When Brillon isn’t building new rods, you’ll find him repairing old ones. Because the process for building a modern bamboo rod hasn’t really changed since Orvis patented the first one back in 1946, Brillion is in the unique position of being able to identify and repair virtually every single bamboo rod the company has ever built and sold.
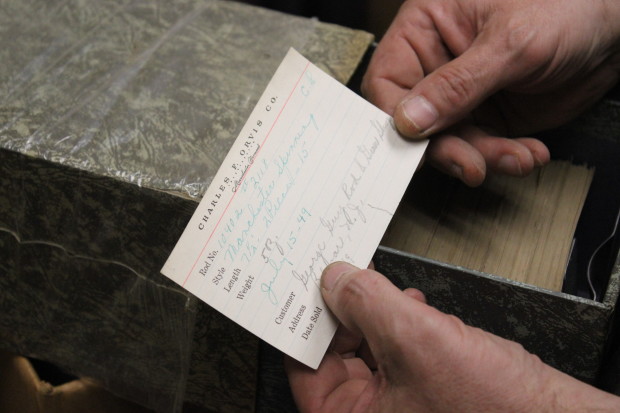
Courtesy Image
In fact, next door to his workshop, Brillon takes us on a tour of Orvis’ records storage, where they’ve kept documentation on file for every single bamboo rod they’ve ever sold to a customer. Brillion says this comes in handy whenever someone finds a dusty, old Orvis rod in a basement or at a yard sale and wants to get it back out on the water.
Tucked away in this room Brillon keeps all the measurements and instructions for building rods that craftsmen have passed down to him through the decades. Some are hand-written, some are type-written, but the records are complete, and if Brillon wanted to repair or rebuild the first rod the company ever sold, he’d have everything he needed to do it right here.
The skills required to reproduce these age-old pieces are even more complex than building a new rod, and Brillon tells us repair times for an antique bamboo pole can take anywhere from six to 12 months. The finished product is a masterful piece of art, however, and one you can take out fishing or proudly display up on the mantle.
from Men's Journal https://ift.tt/Bn1bI3X
No comments:
Post a Comment