An hour south of Portland, Oregon, in a mixed-use neighborhood backed up against Mt. Hood National Forest, is an unassuming two-story building with a large butterfly logo on the front. Adjacent to a large cinema, the country clerk, a few apartments, and a performing arts center, its drab, mall-like exterior isn’t exactly what one envisions when invited to tour the largest knife factory in the country.
Yet, as I would learn, the simple facade is emblematic of what Benchmade Knives stands for: blue collar ethos and a deep attention to customer needs. Inside, the space is much larger than I’d assumed. In total, a 144,000-square-foot facility that houses a small storefront, corporate headquarters, research lab, the factory floor, and distribution. The family-owned knife maker tests, fabricates, and ships all of their products here—spanning tactical, hunting, cutlery, and other specialized lines.
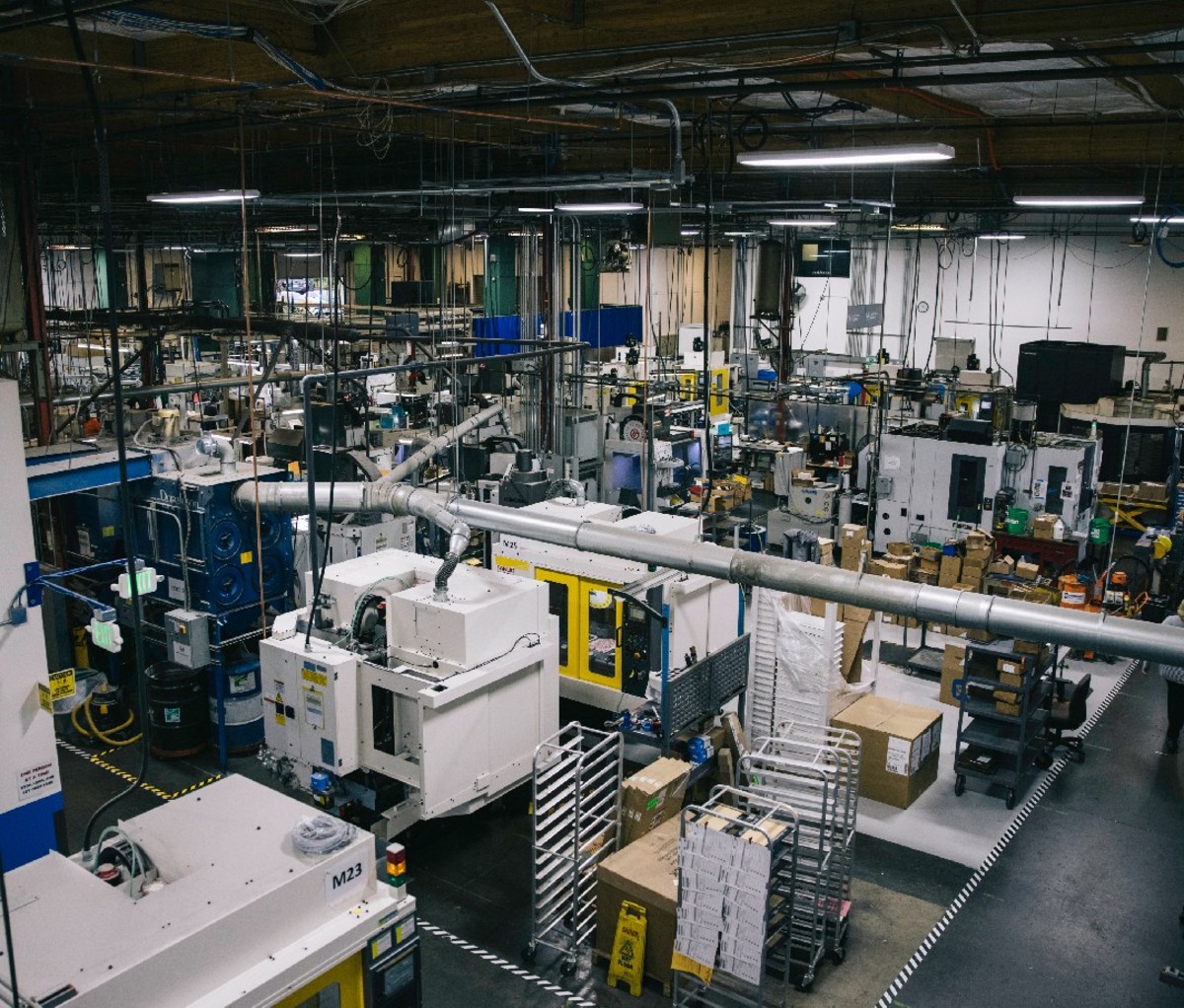
The Beginning of the Benchmade Knife Co.
The Benchmade story started in the late 1970’s, when company founder Les de Asis developed a new version of a Bali-Song knife in a machine shop. As a Filipino growing up in Los Angeles, Les loved the way this knife felt, how easy it was to open with one hand, and how it reminded him of Filipino culture. However, due to the stigma around butterfly knives, few were being made in America at the time.
An entrepreneur at heart, Les picked the name Benchmade to represent the quality he wanted put into every product. He envisioned a large operation with machine-precision parts paired with hand-assembled finished products. From the start, he was committed to making all of their knives in America, often sourcing from local and regional suppliers in Oregon. While he knew hand crafting would drive up costs, Les prioritized a high-end product—and this was the only way to do it. Offshoring wasn’t an option.
Inside the Benchmade Factory
To learn about the technology, materials, and testing behind Benchmade Knives, we took a factory tour to see it for ourselves. Here’s a glimpse into their process, from raw steel to finished knives.
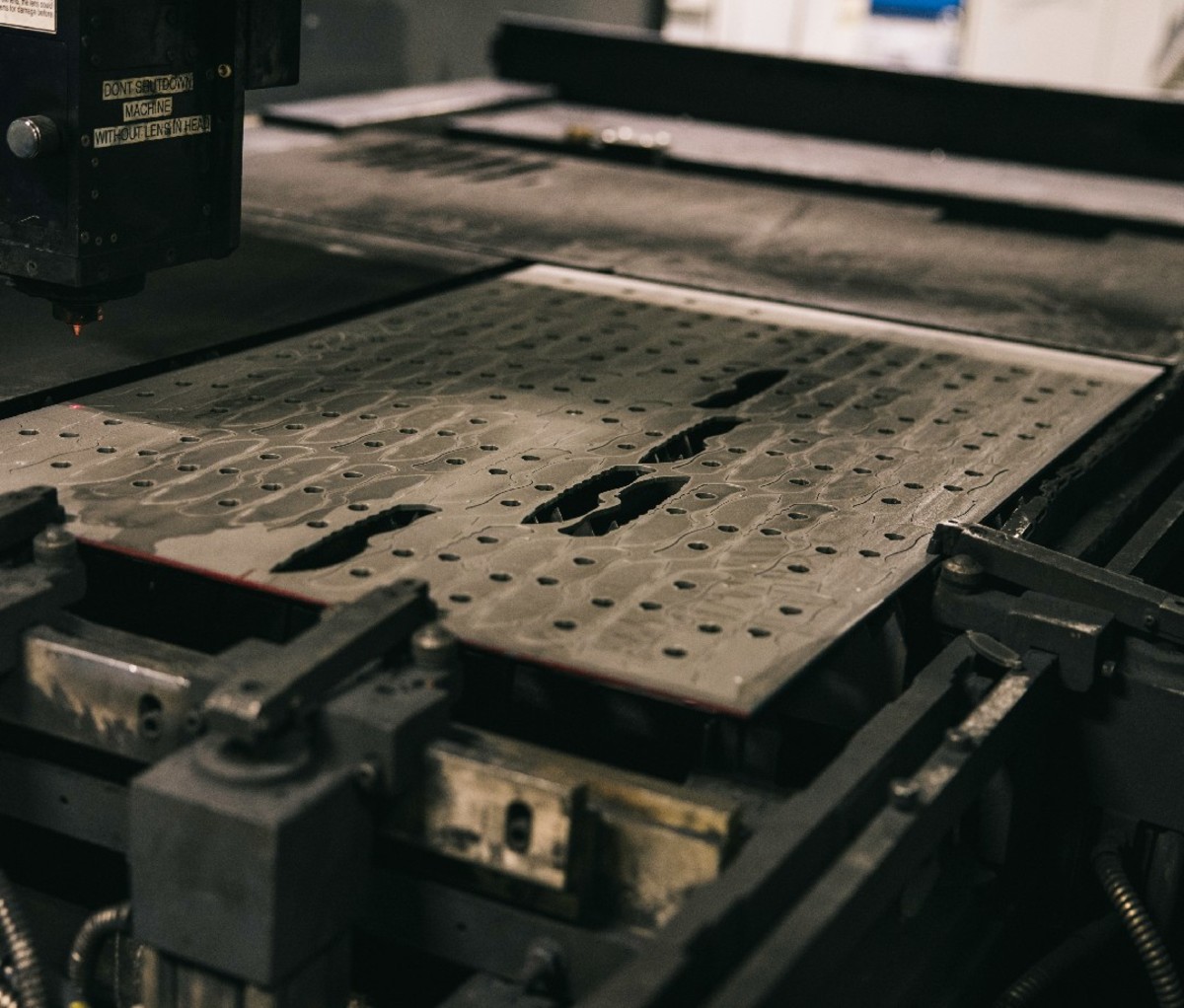
After sourcing alloys with the appropriate stiffness for the end product, the first step in the factory is cutting blades from large sheets of steel. This is done with computer models and a high-powered laser cutter. Benchmade was the first company to use a laser, enabling the cutting of steels too hard to stamp. The process, shown above, may remind you of cutting holiday cookies out of dough, but it’s much more precise. Even the smallest imperfection means the knife will fail the quality control test and not be sold to a customer.
To support dozens of alloys in various knives and thousands of permutations of custom builds, factory workers have become masters of organization and tracking. To meet high demand, teams work in shifts—covering 24 hours a day, six days a week. Each step in the process is meticulously documented from the order initiation to the moment it is boxed and shipped.
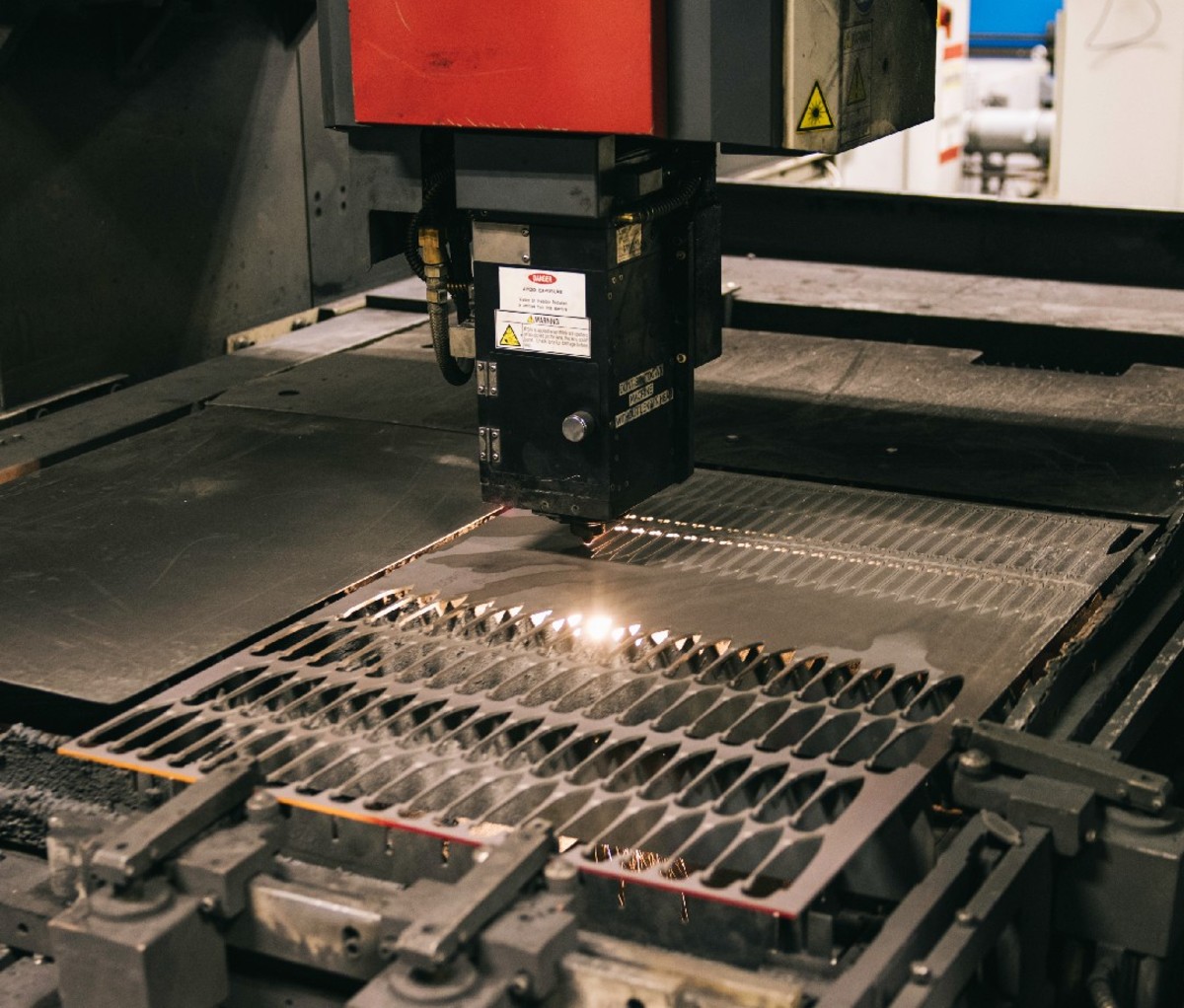
Making a Knife Takes a Village—of Craftspeople, Skilled Technicians, and Machines
Blades then go through a series of machines—most of which perform a single task—for shaping, polishing, and coating. Each is operated by a skilled technician who makes sure the fledgling knife holds the quality standards and specs of the specific build. Through this process the blade is trimmed down to its final form with a bevel, spine, plunge line, and tip. The tolerances accepted are akin to the aerospace industry—often half the width of a human hair and perfect symmetry between the two sides of the knife.
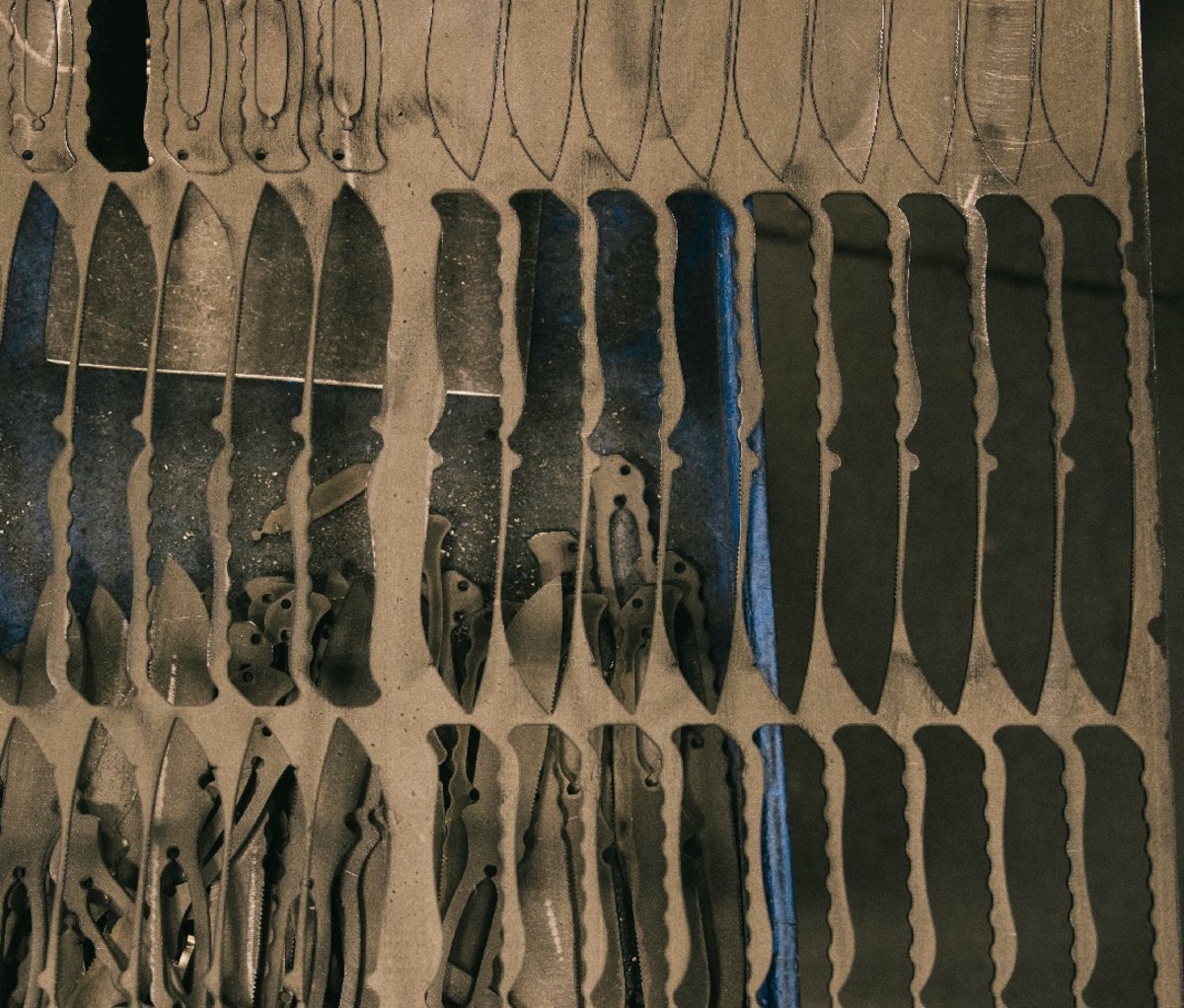
Then come the knife handles, which are made from a variety of materials including wood, carbon, and aluminum. To get the right shape, nearly all are cut with a digitally-guided Computer Numerical Control (CNC) machine. This also allows for knives to have fewer parts, with complex geometries cut out of the same material, often leaving only the rivets, blade, and springs to be installed.
Hand-Assembled and Tested to Perfection
Then comes the assembly process, which varies considerably by the order. This is entirely done by hand, which is as arduous as it sounds. Benchmade offers customization of a handful of knife models, which increases the workmanship complexity even more. A team of a couple dozen craftspeople hand-assemble each knife and test the final product for any imperfections or oddities.
The manufacturing process comes full circle in the research lab, which is one door away from the factory floor. A small team works in the lab to test prototypes, early production runs, and knives that have been sent back to the factory. Their goal is to empirically measure and improve the quality and sharpness that Benchmade is able to produce. This starts at a molecular level for the alloys they source and expands to rigorous testing of full knives, using mostly custom-built machines to assess the decline over thousands of cuts, openings, and stress tests. All of this happens to make sure that Benchmade knives do precisely what they were made for—making the cut in the real world.
from Men's Journal https://ift.tt/3nPmDby
No comments:
Post a Comment